
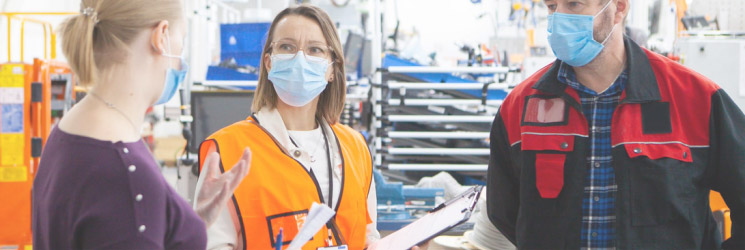
About us
Guidelines for controlling chemical agents
Guidelines for occupational safety and health enforcement 2/2020
Contents
2. Legal basis
3. Definition and characteristics of chemical agents
4. What is monitored
4.1. List of chemicals, safety data sheets, chemical packs and instructions for safe use
4.2. Risk assessment and workplace audit
4.2.1. Written risk assessment of chemical agents
4.2.2. Workplace audit by occupational healthcare provider, action plan and medical examinations
4.3. Assessment of exposure to chemical agents and limit values
4.4. Hazards caused by the physical properties of chemical agents
4.5. Personal protective equipment
4.6. Training and guidance
4.7. First aid and preparedness for emergencies
4.8. Shared workplace
5.1. Caution
5.2. Stop-use order
6. Cooperation and expert activities
7. Period of validity
Annexes
1. Purpose of guidelines
Compliance with the legislation on the control of chemical agents at work is monitored by the occupational health and safety (OHS) authorities. The guidelines provide a description of the measures to be verified and overseen by inspectors in order to ensure that the obligations related to chemical agents are duly complied with in the workplace.1 The guidelines harmonise OHS inspections procedures for chemical agents and increase transparency.
The guidelines provide a general description of the items monitored by OHS inspections, the obligations that may be imposed on employers and how compliance is verified. The guidelines do not address other activities or the exercise of powers, such as criminal cases or administrative sanctions.
Inspectors make an overall assessment of the workplace. These guidelines serves as an aid for inspectors describing the measures to be taken at the inspections.
1 The guidelines do not address the monitoring of the health hazards posed by asbestos.
2. Legal basis
Primary provisions on chemical agents are set out in the Occupational Safety and Health Act (738/2002) and the Government Decree on Chemical Agents at Work (715/2001) issued pursuant to said Act.
OHS inspections are carried out to draw attention to the following provisions in particular:
- Section 8 – Employers’ general duty to exercise
- Section 10 – Analysis and assessment of the risks at work
- Section 11 – Work that causes particular risks
- Section 14 – Instruction and guidance to be provided for employees
- Section 15 – Providing personal protective equipment, auxiliary equipment and other devices for use
- Section 18 – Employees’ general obligations
- Section 20 – Use of personal protective equipment and suitable work clothing
- Section 21 – Use of work equipment and dangerous substances
- Section 33 – Ventilation of workplaces and volume of workrooms
- Section 37 – Airborne impurities
- Section 38 – Chemical agents and dangerous substances used at work
- Section 46 – First aid.
Other regulations related to the control of chemical agents include
- The Decree of the Ministry of Social Affairs and Health on concentrations known to be harmful (654/2020) will be updated as necessary when new information on the harmful effects of chemical agents is obtained.
- Act on the List and Register of People Exposed to Carcinogenic and Mutagenic Substances and Substances Toxic to Reproduction (452/2020), also called the ASA Act.
- The Government Decree on substances at work that are carcinogenic, mutagenic or toxic for reproduction (113/2024) - the Decree applies to work where employees are exposed or may be exposed to substances that are carcinogenic, mutagenic or toxic for reproduction.
- Government Decree on the protection of pregnant workers and workers who have recently given birth, and breastfeeding workers from agents that pose a risk at work (143/2024)
- Occupational Health Care Act (1383/2001)
- Government Decree on medical examinations in work that presents a special risk of illness (1485/2001)
- Government Decree on the principles of good occupational health practice, the content of occupational health care and the educational qualifications required of professionals and experts (708/2013).
The occupational safety and health authority also enforces the Chemicals Act and the provisions issued under it as well as the chemicals legislation of the European Union (e.g. the REACH Regulation and the CLP Regulation) for work where the employer is obliged to comply with the Occupational Safety and Health Act.
3. Definition and characteristics of chemical agents
A chemical agent at work means 2 “any chemical element or compound, on its own or admixed, as it occurs in the natural state or as produced, used or released, including release as waste, by any work activity, whether or not produced intentionally and whether or not placed on the market”.
A hazardous chemical agent means any chemical or exposure agent which may, because of its physico-chemical, chemical or toxicological properties, present a risk to the safety and health of employees. For some chemical agents, an occupational exposure or a biological limit value may be assigned in order to assess and prevent workrelated exposure.
Chemical exposure means a situation in which a chemical agent is present at work and employees come into contact with it. Exposure may take place via inhalation, skin contact or the gastrointestinal tract.3
To have any health effects, the exposure agent or its metabolite must reach a specific target organ in the body. Exposure and its consequences are determined by the level, type and duration of exposure and the employee’s individual qualities and characteristics, such as sensitivity or exposure during off-duty hours. For example, smoking multiplies the harmful effects of dusts in the body. The combined effect of chemical and physical factors may intensify the ill-effects of exposure, for instance, exposure to solvents in noisy conditions may increase the risk of hearing damage.
Chemical agents may have both short and long-term health effects:
- The effects may be acute appearing at the time of exposure or soon after it.
- An exposure agent may be accumulated in the employee’s body.
- The effects of work-related exposure may be latent, emerging years or decades later.
Excessive exposure to hazardous chemical agents may lead to adverse health effects or occupational diseases. At its mildest, the ill-effect may only cause temporary irritation. Serious ill-effects may be caused by respiratory or skin sensitising, acutely toxic or corrosive, mutagenic or reprotoxic hazardous chemical agents and agents posing a risk of germ cell toxicity.
2 Government Decree on Chemical Agents at Work (715/2001)
3 Decree of the Ministry of Social Affairs and Health on Hazardous Concentrations (654/2020)
4. What is monitored
Employers are required to comply with the occupational health and safety legislation and the general duty of care defined in it.
Inspectors supervise that employers comply with the occupational health and safety legislation and the general duty of care defined in it with due regard to the following principles:
- There is sufficient awareness of employees’ exposure to chemical agents, any hazards are eliminated and risks minimised so as to ensure that the health of workers is not compromised.
- Adequate measures have been taken to ensure the health and safety of employees with due regard to the specific circumstances related to the work, working conditions and other relevant circumstances as well as the personal skills and characteristics of the employees.
- The measures required to improve working conditions have been duly planned, selected, adjusted to local conditions and implemented.
- The working environment, the safety of the working methods and the impact of the measures taken on occupational health and safety is monitored continuously.
Inspectors verifies that employers have eliminated risks in the pre-determined order of priority using the following methods:
- Substitution: the hazardous substance has been eliminated or substituted with a less hazardous alternative.
- Technical and structural measures: the concentration of the hazardous agent has been minimised in the exposure zone, for example by providing efficient ventilation. The same applies to exposure agents generated or present at work, such as smoke, fumes, vapours and dust.
- Organisational measures: the number of employees exposed and/or the duration and intensity of exposure have been minimised.
- Personal protective equipment is the last recourse in the efforts to prevent exposure: exposure is prevented using protective clothing or wearing protective equipment, such as goggles, gloves or respirators as a barrier to exposure. If the hazard is associated with a carcinogenic, mutagenic or toxic to reproduction agent, the limit values set for the agents are binding.
The inspector uses appropriate methods to verify compliance with the employer’s general duty of care with due regard to the workplace as a whole and the nature of the inspection being carried out, particularly in respect of the following:
- Exposure agents generated and present at work
- List of chemicals, safety data sheets, chemical packs and instructions for safe use
- Risk assessment of chemical agents and a workplace audit by the occupational healthcare provider
- Assessment of exposure to chemical agents and limit values
- The employer-specific obligation to keep a list of carcinogenic and mutagenic agents and those toxic to reproduction as well as notifications to the ASA Register 4
- Hazards caused by the physical properties of chemical agents
- Personal protective equipment (PPE)
- Training and guidance
- Shared workplace
- First aid and preparedness for emergencies.
The inspector verifies compliance with the measures specified in the risk assessment, particularly if sensitising, carcinogenic, mutagenic or reprotoxic (CMR) or acutely toxic chemical or exposure agents are used or generated at work.5
4 ASA Register (in Finnish). The Finnish Institute of Occupational Health.
ASA-classified exposure agents: The employer must report all substances that are Carc.1A/1B classified under the EU CLP Regulation (hazard statements H350 or H350i) or substances that are Muta.1A/1B classified as germ cell mutagenic (hazard statement H340) and the working methods listed in Annex 1 to Government Decree 113/2024.
Employees to the reported to the ASA Register
If no detailed information on exposure levels is available, employers are to report to the ASA Register employees who have carried out work involving exposure to a carcinogenic, mutagenic or reprotoxic agent for a significant number of hours per day (at least 2 hours per day) during 20 workdays in the year concerned or an equivalent period of time (e.g. 1 hour over a period of 40 days).
Employers’ listing and notification obligations related to exposure agents to be reported to the ASA Register
The employer must keep a list of carcinogenic, mutagenic and toxic to reproduction agents used or present in the workplace, and the workers exposed to these. The employer must report the names of the employees who have been exposed to carcinogens and mutagens by the end of March each year to be entered in the Finnish Institute of Occupational Health's national ASA register.
ASA code
ASA registration is based on the ASA codes available on the relevant webpage of the Finnish Institute of Occupational Health: ASA Register (in Finnish).
ASA Register
The Finnish Institute of Occupational Health maintains the ASA Register to which employers are required to report the data listed above. The register data is used as a basis for an annual statistical overview and harnessed in occupational health research.
4.1. List of chemicals, safety data sheets, chemical packs and instructions for safe use
Employers must have in place an updated list of the trade names of the chemicals used at the workplace. As well as the trade names and classification data, the chemicals list7 must indicate whether a safety data sheet is available for the chemical.
The safety data sheet and accompanying exposure scenario (ES) provide information on the safe use of the chemical, such as prevention of exposure, personal protective equipment and first aid. The safety data sheet sheets must be provided in Finnish or Swedish, be up-to-date and readily accessible to employees, for example in hardcopy format, or in the form of electronic links readily available and readable at the workplace. The links must remain updated and operational so as to ensure that the supplier’s responsibility for his own product remains in force for a sufficiently long period of time after the delivery of the chemical.
The markings on the chemical packs and consumption containers must be easily readable in Finnish and/or Swedish and only apply to the chemical concerned.
The ways in which the chemical can be used safely are described in the safety data sheet, or if appropriate, the instructions for safe use can be prepared in-house.
4.2. Risk assessment and workplace audit
With regard to chemical agents, the parts of the risks assessment to be made by the employer can be described as follows:
- Analysis and identification of the risks
- Assessment of the significance of the risks
- Determination of the measures to eliminate and reduce risks
- Implementation of the measures
- Monitoring of the impacts of the measures.
Planning to be carried out by the occupational healthcare provider must be based on a workplace audit, which must draw upon the in-house risk assessment made by the employer.
As far as hazardous chemical and exposure agents are concerned, both the employer’s risk analysis and assessment and the workplace audit carried out by the occupational healthcare provider must address all workplace activities and tasks.
5 Respiratory sensitising chemicals cause respiratory hypersensitivity when inhaled. Skin sensitising chemicals cause
skin allergy.
Carcinogenic chemicals may cause cancer in humans or test animals.
Mutation is a permanent hereditary genetic alteration or an alteration in the DNA. The term ‘mutagenic’ and ‘mutagen’ is used for agents giving rise to an increased occurrence of mutations in populations of cells and/or organisms.
Reproductive toxicity: Reproductive toxicity includes adverse effects on sexual function and fertility in humans, as well as developmental toxicity in the offspring.
Acutely toxic substances are substances that produce significant toxicity in humans, or that, on the basis of evidence from studies in experimental animals can be presumed to have the potential to produce significant toxicity in humans following single exposure.
6 The classification data required under the CLP Regulation refers to hazard class, category and hazard statements
4.2.1. Written risk assessment of chemical agents
The risk assessment of chemical agents will be prepared in writing with due regard to the following:
- The significance of the hazards to employee health and safety is assessed comprehensively, for example by analysing each chemical agent at the workplace specifically to each workstation or process.
- All the permanent or temporary employees within the sphere of influence of the workplace, particularly special groups, such as pregnant and young employees, should be considered.
- Occupational diseases, injuries, accidents and close calls that have occurred in the workplace.
- The risks determined and measures planned should be sufficient to prevent employee exposure and proportionate to the risks posed by the exposure agents.
- Working methods should be designed and organised for maximum safety including general hygiene and the disposal, storage and transport of wastes.
- Employees should be provided with adequate equipment and tools suitable for the job at hand that do not increase the level of risk or exposure.
- Safety ways of working should be described and instructions provided.
The risk assessment should be updated when necessary. Employees should be provided with the information required for the assessment as well as additional information whenever the situation changes.
4.2.2. Workplace audit by occupational healthcare provider, action plan and medical examinations
The provision of occupational healthcare services is supervised as provided in the supervisory guide7.
The occupational healthcare provider’s workplace audit and action plan must be in written format and up-to-date and draw upon the employer’s in-house risk assessment.
As far as chemicals and chemical agents are concerned, the occupational healthcare provider’s audit and plan must address all workplace activities, exposure agents and medical examinations. The audit and plan must assess the significance of the risks and hazards to the health and safety of differently exposed employees, and work duties involving a special health hazard must be identified and the need for medical examinations recognised.8
7 Guidelines for occupational safety and health enforcement: Control of the provision of occupational healthcare.
8 Guidelines for occupational healthcare: Exposure-based occupational health and safety monitoring, Duodecim.
4.3. Assessment of exposure to chemical agents and limit values
Air pollution or biological exposure measurements must be carried out when there is a reason to believe that exposure hazardous to health occurs and the employer is unable to demonstrate the safety of work in other ways, such as by means of simulations.
The employer must organise the measurements and assess exposure conditions as well as assume responsibility for the measures to be taken in response to the assessment.
4.4. Hazards caused by the physical properties of chemical agents
Chemical agents must be stored and handled safely with due regard to the need to separate incompatible chemical agents. The purpose of the measures is to protect employees from hazards due to fire, explosions, etc.
Responsibility for the supervision of explosive atmospheres is shared by several authorities: The occupational health and safety authorities supervise the safety of work referred to in the Occupational Safety and Health Act which may involve hazards due to explosive air mixtures. The Finnish Safety and Chemicals Agency (Tukes) supervises facilities which handle and store chemicals in large quantities subject to authorisation under the Act on the Safety of Handling Hazardous Chemicals and Explosives. The rescue authorities supervise facilities which handle and store chemical in low quantities.
ATEX (atmosphères explosibles) statutes apply to all employers whose employees may be exposed to explosion hazards due to flammable liquids, gases or dust. Employers are required to classify explosive atmospheres, mark such premises with EX, prepare an explosion protection document and take the necessary precautions against explosions in all work and production processes as well as equipment selections.9 10 11
9 A specific decree (576/2003, in Finnish) has been issued on the prevention of workplace hazards caused by explosive air mixtures. The purpose of the decree is to prevent hazards and protect the health and safety of employees as well as to maintain a general level of safety and prevent injuries and damage to property.
Employers are required to ensure the health and safety of employees working in explosive atmospheres. Employers are required to take the measures necessary for safe working in explosive atmospheres. Additionally, employers must duly monitor explosive atmospheres using technical means. For more information: ATEX. Tyosuojelu.fi.
10 For more information (in Finnish): Accident-hazardous work. Finnish Institute of Occupational Health.
11 Responsibility for the supervision of the use and storage of hazardous chemicals – i.e., licenses, notifications, commissioning and in-service inspections – is shared by Tukes and rescue services depending on the type and quantities of chemicals handled and stored. For more information: Potentially explosive atmospheres. Finnish Safety and Chemicals Agency (Tukes).
4.5. Personal protective equipment
If the work arrangements, working methods or general protective measures to prevent exposure by structural and technical means are not enough to ensure safety, it is necessary to wear personal protective equipment.
Employees must have access to personal protective equipment selected on the basis of the risk assessment and consistent with the requirements laid down by law. The equipment must be personal and suitable for the job at hand and stored and serviced appropriately between work periods. The personal protective equipment must remain serviceable at all times. Workplaces must have in place procedures to ensure that the protective equipment selected for use is effective when worn by the employee, suitable for the employee’s state of health and ergonomically fitting.
Protective equipment designed for different uses must be suitable for the job at hand and mutually compatible to ensure, for example, that the incompatibility of goggles with hearing protectors, or an edge-seal leakage caused by the beard, or ill-fitting protective gloves when handling solvents, do not increase exposure.
4.6. Training and guidance
Training and guidance must be provided as required by the type of work and workplace conditions necessary in order to avoid accidents and work-induced illnesses.
The training must provide information included in the risk assessment on the identification of risks due to chemical agents, such as:
- exposure agents generated and present at work
- safe use and handling of chemicals
- risks to health and safety, potential interactive effects, occupational exposure limits
- safety data sheets, labelling and other instructions for safe use
- selection, use, storage and servicing of protective equipment suitable for intended use
- rescue-related measures (such as the use of escape protectors).
Employers must see to it that employees understand the instructions given to ensure that employees with a foreign mother tongue know how to work safely.
4.7. First aid and preparedness for emergencies
Employers are required to provide adequate first aid capabilities based on the in-house risk assessment.
If appropriate, employers must have in place an action plan to respond to hazards and emergencies caused by chemical agents and accidents in order to prevent dangerous exposure.
Adequate instructions must be provided and a sufficient number of people with firstaid skills available in all shifts. If necessary, a specific area or first-aid site near the hazard source must be designated for the administration of first aid. The workplace must have sufficient first-aid equipment and tools in serviceable condition, properly stored and readily available in marked locations.
If the risk of accident cannot be fully eliminated, workplaces must have a sufficient number of readily available aids and tools in serviceable condition for first-aid purposes and to respond to accidents and prevent and collect spills, such as extra an oxygen supply, emergency shower, eye washer, portable respirator, escape device or neutralisation agent and oil absorbent materials.
4.8. Shared workplace
The employer exercising the main authority at a shared workplace must ensure that the external employers organising work at the workplace and their employees have received the necessary information and instructions on the hazards and risk factors concerning the work at the workplace as well as coordinate on-site activities so as to ensure safety.
Both the external employers and the self-employed workers must inform the employer exercising the main authority and other employers of the hazards and risk factors that may be caused by their work.12
12 Sections 50 and 51 of the Occupational Safety and Health Act
5. Employer’s obligations
Inspectors make an overall assessment of the workplace and evaluate the employer’s capabilities to manage the risks associated with chemical agents.
Inspectors are authorised to issue instructions, cautions or temporary stop-use orders. Compliance with the obligations and the exercise of supervisory powers are monitored in accordance with the OHS guidelines.13
13 Guideline on occupational safety and health enforcement and the use of authority (2021)
5.1. Caution
A caution may be issued, inter alia, in the following cases:
No written risk assessment has been made.
An employee is exposed to risk and the employer has failed to take action to prevent it.
No reliable risk assessment has been carried out. In the foregoing cases, the employer will be asked to obtain the missing information and complete the risk assessment. Shortcomings may, for example, relate to safety data sheets and/or list of chemicals. The caution will be accompanied by instructions or, if necessary, an admonition to complement the risk assessment.
The work poses a special risk of disease or illness, risk management arrangements are inadequate or the requisite protective measures have not been taken.
No ASA list has been prepared. No workplace audit prepared by the occupation healthcare provider has been prepared or it fails to address chemical agents as exposure sources or chemical risks at work when it involves exposure to hazardous chemical agents.
Work duties involving a special risk of illness have not been identified, nor the need for medical examinations recognised in the occupational healthcare provider’s workplace audit or action plan, or medical examinations related to a special illness risk have not been carried out.
The physical properties of chemical agents pose a risk; for example, there are shortcomings in the storage, handling or separation of incompatible chemical agents.14
Employees have not been adequately trained and instructed in the safe use of chemicals or the management of the risks associated with chemical agents, and the employees lack the skills and capabilities required for protection against, or safe use of, chemical agents. Serious shortcomings in training and guidance are based on the observations made by the inspector concerning hazardous or risky ways of working or modes of operation, etc.
The technical or other primary measures taken in the exposure zone are inadequate, and adequate actions to ensure the personal protection of employees have not been taken. Example:
- Adequate personal protective equipment has not been made available to employees
- No instruction or guidance has been given in the use of personal protective equipment
- Employer fails to supervise the use of protective equipment.
With regard to measurements and prevention of exposure, a caution may be issued, inter alia, in the following cases:
- Work hygiene measurements necessary for ensuring safety or required by an inspector on an earlier occasion have not been carried out, no assessment of exposure risks has been made and risk management is not up to the required standard.
- Exposure levels estimated on the basis of duly made work hygiene concentration measurements exceed the binding limit value or HTP value.
- The results of biological exposure measurements are exceeded relative to the biological reference values more than insignificantly.
- Inspectors have other well-founded reasons to believe that the existing exposure levels pose a risk.
14 Compliance with the Government Decree on the Supervision of the Handling and Storage of Hazardous Chemical Agents (685/2015) is not monitored by the occupational health and safety authorities.
5.2. Stop-use order
If a defect or shortcoming at the workplace endangers the life or health of an employee, exposure to such a risk must be stopped.
The OSH authority may issue a stop-use order until the non-compliant conditions have been remedied or eliminated.
If the risk is immediate, the inspector may issue a temporary stop-use with immediate effect. Example:
- Risk management of CMR substances is flawed
- Exposure levels exceed the binding limit value.
When the immediacy of the risk is assessed, there must be a strong, well-founded suspicion that the exposure agent is present in the workplace atmosphere in dangerous concentrations and that exposure at the workplace has not been duly and reliably prevented.
6. Cooperation and expert activities
Occupational health and safety supervision is exercised in collaboration with other authorities in accordance withe general guidelines for supervision.15
Occupational healthcare
For the purposes of assessing occupational health issues related to chemical agents, the appropriate partner is the occupational healthcare provider.
Finnish Institute of Occupational Health (FIOH)
The Finnish Institute of Occupational Health offers expert assistance in chemical safety matters and makes available safety-enhancing information sources. For more information: Finnish Institute of Occupational Health, Occupational safety -webpages (in Finnish) by Finnish Institute of Occupational Health.
Finnish Safety and Chemicals Agency (Tukes)
Tukes offers advisory services on compliance with the REACH, CLP and biocide regulations. Tukes’ KemiDigi is a national chemicals database used for collecting national chemical data. Storage and handling of large quantities of hazardous chemicals is supervised by Tukes. Storage and handling of low quantities of chemicals is supervised by the rescue authorities.
Reports to Tukes
Any non-compliant safety data sheets, chemical packs or other clear violations of the Chemicals Act or legislation concerning the placement on the market of chemicals must be reported to Tukes ([email protected]). The report must be accompanied by the details of the chemical obtained from the employer:
- classification
- use of the chemical and quantities involved
- is the chemical in frequent use in the company?
Additionally, the report may be accompanied by readily available information on the properties of the chemical:
- place and date of purchase of the chemical
- safety data sheet: was it included in the delivery?
- is the chemical imported by the company itself?
- information on the supplier/manufacturer of the chemical.
The report may be accompanied by photographs.
Centre of Excellence for Serious Chemical Threats
The Centre of Excellence for Serious Chemical Threats (C Centre) is a collaborative network coordinated by the Finnish Institute of Occupational Health and tasked to support preparedness against chemical threats and to maintain a chemical hazard oncall service to assist the authorities responsible for the emergency response system in case of threats. As part of these activities, the Finnish Institute of Occupational Health maintains regional field teams which can be deployed to incident sites for the purpose of collecting samples and evaluating the situation. Additionally, the C Centre maintains a list of laboratories that can provide chemical analysis services necessary for responding to incidents and emergencies.
In chemical incidents posing a potential health risk, the C Centre telephone service offers expert assistance in identifying the agent in ambiguous cases, assessing the level of exposure and health risk, taking protective measures and other decision-making necessary for dealing with the situation, as well as provides background information for public communications purposes.
Other services offered by the C Centre includes post-incident advice, such as the assessment of potential follow-up needs (exposed population, employees). The on-call services provided by the C Centre are organised jointly by the Institute of Occupational Health and the National Institute for Health and Welfare. The telephone number intended for official use is 0800 411 415. In less urgent cases, contacting takes place in accordance with the instructions given on the C Centre’s website (in Finnish).
Poison Information Centre
The Poison Information Center answers questions by phone (at 0800-147111 and 09-471977) concerning the prevention and treatment of acute poisonings around the clock. During office hours, the Center serves as an information resource for the authorities and the media.
15 Guideline on occupational safety and health enforcement and the use of authority (2021)
7. Period of validity
The Guide is valid up until 31 December 2025.
Annexes
Other items to be checked
REACH Regulation
Regulation (EC) No 1907/2006 of the European Parliament and of the Council on the Registration, Evaluation, Authorisation and Restriction of Chemicals (REACH Regulation) Provisions on national supervision of compliance with the REACH Regulation are set out in the Chemicals Act (599/2013).
The occupational health and safety authority is the competent authority supervising compliance with the REACH Regulation with regard to the following (section 10 of the Chemicals Act, 599/2013):
The recognised use of the substance, the permit number of a substance subject to authorisation indicated in sections 1 and 2 of the safety data sheet
If substances subject to prohibitions or restrictions are being used at the workplace, the employer must, if necessary, demonstrate that all license conditions, restrictions and prohibitions are complied with.
Exposure scenario (ES) accompanying an extended safety data sheet
The exposure scenarios contain information on the safe use of chemicals and risk management and waste disposal measures, based on chemical safety assessments carried out under the REACH Regulation. If necessary, the employer must demonstrate to the inspector that the chemicals are safe to use.
The substance registration number indicated in section 1 of the safety data sheet
If appropriate, the employer must demonstrate that the agents used at work are registered as required under the REACH Regulation, unless the agent has been exempted from registration or it has been imported into the country in quantities falling short of the registration limit.
Annex XIV to the REACH Regulation ‘List of substances subject to authorisation’
If appropriate, employers must demonstrate that the substance subject to authorisation is being used in compliance with the applicable conditions.
Annex XVII to the REACH Regulation ‘Restrictions on the manufacture, placing on the market and use of certain dangerous substances, mixtures and articles’
When the substance is used at work, the occupational health and safety authority may, if necessary, intervene in case of clear and material violations by preventing the substance from being placed on the market and released for use in the manner specified in the Act on Occupational Safety and Health Enforcement and Cooperation on Occupational Safety and Health at Workplaces (44/2006).
Compliance with the obligations and the exercise of supervisory powers are monitored in accordance with the Act on Occupational Safety and Health Enforcement and Cooperation on Occupational Safety and Health at Workplaces (44/2006) and the OHS guidelines. Any suspected breaches of law in REACH-related matters are reported to Tukes [email protected].
Concepts, references
Framework Directive on occupational health and safety
Occupational health and safety legislation represents fully harmonised community law.
Council Directive 89/391/EEC on the introduction of measures to encourage improvements in the safety and health of workers at work. Consolidated version of 11 December 2008 at EUR-Lex website.
The occupational health and safety authority supervises employers’ compliance with their statutory obligations.
CAD Directive, Chemical Agents Directive 98/24/EC
Council Directive 98/24/EC on the protection of the health and safety of workers from the risks related to chemical agents at work (fourteenth individual directive within the meaning of Article 16(1) of Directive 89/391/EEC), as amended. Consolidated version of 26 July 2019 at EUR-Lex website.
CMD Directive, Carcinogens or Mutagens Directive 2004/37/EC
Directive 2004/37/EC of the European Parliament and of the Council on the protection of workers from the risks related to exposure to carcinogens or mutagens at work, as amended. Codified version of 5 April 2022 at EUR-Lex website.
STOP Principle: order of priority of control measures in preventing or reducing exposure
The EU Chemical Agents Directive (CAD) specifies a hierarchy or ‘order of priority’ of control measures to prevent or reduce the exposure to dangerous substances. STOP is an acronym based on English words.
- S (Substitution) = Substitution if possible - elimination or substitution of the dangerous substance with a safer alternative
- T (Technological) = Technological measures – minimising the concentration of the dangerous substance in the exposure zone
- O (Organisational) = Organisational measures – minimising the number of exposed workers and/or the duration and intensity of exposure
- P (Personal protective measures) = wearing protective clothing or equipment such as goggles and gloves as a barrier to exposure.
The same order of priority is followed in Finnish occupational health and safety legislation.
Standard SFS-EN 689:2018 + AC:2019 Workplace exposure. Measurement of exposure by inhalation to chemical agents. Strategy for testing compliance with occupational exposure limit values strategy
A standard for assessing exposure to chemical agents by inhalation by means of llimit values and a strategy for testing. The standard has been adopted by the European Committee for Standardization. The standard provide detailed information on the testing strategy and the interpretation of measurement results.
REACH Regulation
Original version at EUR-Lex website.
REACH Regulation, consolidated version of 17 December 2022 at EUR-Lex website.
The consolidated version does not include the introduction, which is only contained in the original REACH Regulation.
It is advisable to consult the annexes to the REACH Regulation using the latest consolidated version (e.g. Annex XIV ‘List of substances subject to authorisation’ and Annex XVII ‘Restrictions on the manufacture, placing on the market and use of certain dangerous substances, mixtures and articles’).
Reach Regulation contains provisions on safety data sheets
The supplier of a substance or mixture must provide the recipient of the substance or mixture with a safety data sheet compiled in accordance with Annex II of the REACH Regulation.
All safety data sheets prepared or updated after 1 June 2015 must meet the requirements set out in the new version of the (EU) 2015/830 Regulation. As of 1 June 2015, all substances and other mixtures must be classified and labelled in accordance with the CLP Regulation. After 1 June 2017, only the safety data sheets complying with the annex of the (EU) 2015/830 Regulation are acceptable for substances and mixtures.
Safety data sheet to be accompanied by an exposure scenario
Exposure scenario means the set of conditions, including operational conditions and risk management measures, that describe how the substance is manufactured or used during its life-cycle and how the manufacturer or importer controls, or recommends downstream users to control, exposures of humans and the environment. These exposure scenarios may cover one specific process or use or several processes or uses as appropriate. Use and exposure category means an exposure scenario covering a wide range of processes or uses, where the processes or uses are communicated, as a minimum, in terms of the brief general description of use.
According to Article 31, subsection 7, of the REACH Regulation, any actor in the supply chain who is required to prepare a chemical safety report shall place the relevant exposure scenarios in an annex to the safety data sheet.
CLP Regulation, Regulation (EC) No 1272/2008 of the European Parliament and of the Council of on classification, labelling and packaging of substances and mixtures
Original version at EUR-Lex website.
CLP Regulation, consolidated version of 17 December 2022 at EUR-Lex website.
The consolidated version does not include the introduction, which is only contained in the original CLP Regulation.
The regulation requires manufacturers, importers and downstream users of the substances and mixtures to classify, label and package dangerous chemicals appropriately before placement on the market. Tukes serves as the competent authority for the purposes of the CLP Regulation.
The CLP Regulation specifies detailed criteria for the markings: pictograms, signal words and hazard statements as well as statements concerning prevention, measures, storage and waste disposal for each hazard class and category. Additionally, the regulation sets out the general packing standards designed to ensure the safe delivery of dangerous substances and mixtures.
In the CLP Regulation, old concepts have been replaced by new ones:
- Products have been replaced by mixtures.
- Hazard (H) statements have been replaced by risk (R) phrases.
- Safety-related S-phrases have been replaced by P-phrases.
Classification of chemicals
For more details, see for example Tukes website (in Finnish).
The hazard classes in CLP cover physical, health, environmental and additional hazards. Under the CLP Regulation, substances or mixtures are assigned to the following hazard classes and categories according to the applicable criteria:
- Acute toxicity (oral, dermal and by inhalation), hazard category 3
- Skin corrosion / irritation
- Serious eye damage/eye irritation
- Respiratory sensitizer (respiratory tract, skin)
- Germ cell mutagenicity
- Carcinogenicity
- Reproductive toxicity
- Specific target organ toxicity (STOT): single and recurring exposure
- Aspiration hazard.
Hazard statements according to the CLP Regulation are available at Tukes website (pdf, in Finnish).
Hazard classes and categories:
Acute toxicity
Substances that have produced significant toxicity in humans, or that, on the basis of evidence from studies in experimental animals can be presumed to have the potential to produce significant toxicity in humans following single exposure.
Skin corrosion / irritation
Skin corrosion means the production of irreversible damage to the skin; namely, visible necrosis through the epidermis and into the dermis, following the application of a test substance for up to 4 hours. Corrosive reactions are typified by ulcers, bleeding, bloody scabs and, by the end of observation at 14 days, by discoloration due to blanching of the skin, complete areas of alopecia and scars. Histopathology shall be considered to discern questionable lesions. Skin irritation means the production of reversible damage to the skin following the application of a test substance for up to 4 hours.
Serious eye damage or eye irritation
Serious eye damage means the production of tissue damage in the eye, or serious physical decay of vision, following application of a chemical to the anterior surface of the eye, which is not fully reversible within 21 days of application. Eye irritation means effects that are fully reversible. Skin corrosion is taken into account when the effects on the eye are classified. With regard to eye damage or eye irritation, chemicals are assigned to category 1 or 2.
Respiratory sensitizer (respiratory tract, skin)
Respiratory sensitising chemicals cause respiratory hypersensitivity when inhaled. Skin sensitising chemicals cause skin allergy. Sensitising potential through inhalation and sensitising potential through skin are separate categories. Categories 1, 1A or 1B exist for both effects. A chemical can be classified into sub-category 1A or 1B according to the intensity of the sensitizing effect.
Germ cell mutagenicity
Mutation is a permanent hereditary genetic alteration or an alteration in the DNA. The term ‘mutagenic’ and ‘mutagen’ is used for agents giving rise to an increased occurrence of mutations in populations of cells and/or organisms. Genotoxicity tests are used to demonstrate mutagenic effects. With regard to germ cell mutagenicity, chemicals are assigned to category 1A, 2B or 2.
Carcinogenicity
Carcinogenic chemicals may cause cancer in humans or test animals. Substances which have induced tumours in experimental studies on animals are presumed to act as human carcinogens unless there is strong evidence that the mechanism of tumour formation is not relevant for humans. With regard to carcinogenicity, chemicals are assigned to category 1A, 2B or 2.
Reproductive toxicity
Reproductive toxicity includes adverse effects on sexual function and fertility in humans, as well as developmental toxicity in the offspring. With regard to reproductive toxicity, chemicals are assigned to category 1A, 2B or 2.
Specific target organ toxicity (STOT): single and recurring exposure
Specific target organ toxicity is defined as a specific harmful effect on a target organ due to single or recurring exposure to a chemical. Harmful effects include all significant health effects that can impair function, both reversible and irreversible, immediate and/or delayed and that are not addressed by other hazard classes. These effects are changes which have affected the function or morphology of a tissue/organ, or have produced serious changes to the biochemistry or haematology of the organism and are relevant for human health. Assessment should take into consideration significant changes in a single organ or biological system as well as generalised changes of a less severe nature involving several organs. With regard to target organ toxicity, chemicals are classified into categories 1 or 2, or category 3 in case of single exposure when it results in respiratory irritation or narcotic effects.
Aspiration hazard
Aspiration means the entry of a liquid or solid chemical directly through the oral or nasal cavity, or indirectly from vomiting, into the trachea and lungs. Aspiration toxicity involves severe acute effects such as chemical pneumonia, varying degrees of pulmonary injury or death. With regard to aspiration hazard, chemicals are classified into category 1, the only category used.
Pictograms
Chemical hazards are indicated by markings and signal words and pictograms in safety data sheets. For more information: Hazard pictograms for chemicals. Finnish Safety and Chemicals Agency (Tukes).
CMR substance
A substance defined as carcinogenic, mutagenic or reprotoxic in the manner described above.