
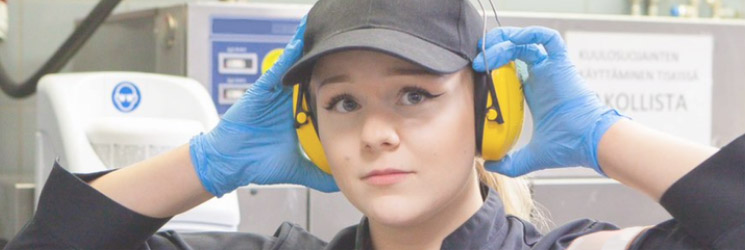
Working conditions
Lighting
General information on topic
What constitutes adequate lighting
The requirements for adequate lighting include, among others, the following:
- Areas that are regularly used by workers usually need to have a minimum light level of 200 lux.
- Enough light must be provided to make out details, taking into account
- the size of the details in question, such as font size
- the age of the employee in question (workers over the age of 45 require more light), and
- how well the details stand out from their surroundings.
- Light sources must be correctly positioned and angled so as to prevent glare, reflections or distracting shadows across access routes or objects and to bring out the shape of the object being worked upon.
- Lights make the workspace easier to perceive by illuminating all surfaces evenly and showing colours as naturally as possible.
- The brightness of surfaces decreases gradually with distance.
- The colour of lights enables workers to see objects clearly.
- There are no sudden changes in lighting between adjacent rooms or areas.
Lighting assessment
It is the employer’s duty to ensure that the workplace is properly lit for the type of work performed there and the workers’ requirements and needs.
The employer may use the guideline values presented in standard SFS-EN 12464-1 to assess indoor lighting. The standard provides certain guidelines for how much light should be available for various tasks and work areas depending on the employee's age. In addition, the standard provides guidance on limiting glare, the aiming and uniformity of light and colour rendering.
Light fittings
Light fittings in workspaces, corridors and other areas of the workplace must be designed so as to not increase the hazards and risks posed to workers.
Outdoor lighting
It is the employer’s responsibility to provide outdoor lighting if daylight is insufficient for workers to be able to move around and perform their work outdoors safely and comfortably.
Guideline values for outdoor lighting are included in SFS-EN 12464-2, Light and lighting. Lighting of work places. Part 2: Outdoor work places. The recommended level of outdoor lighting is between 20 and 50 lux.
Emergency lighting
In some cases, employers have a responsibility to provide emergency lighting to enable any ongoing work to be completed and for workers to exit the workplace safely in the event of a power cut. Emergency lighting must be provided if work is performed underground or in a windowless space or if a power cut could pose a particular risk to workers’ safety.
Servicing and maintenance of light fittings
Light fittings produce less and less light as they become older, and dirt on surfaces can make a space appear darker. It is the employer’s duty to ensure that lights, windows and all surfaces in the workplace are cleaned regularly and that light sources are replaced after a certain period of time. Any blown light bulbs must be replaced immediately.
As most light fittings need to be serviced off the floor, safe access to light fittings must be provided and it must be possible for maintenance works to be carried out safely.
Portable lights
Sometimes the only option is for workers to carry portable lights. This can be the case, for example, when work needs to be performed underground or in other conditions where no other source of light can be provided or cannot be provided at a reasonable cost.
Optical radiation
Light sources generate artificial optical radiation. Provisions on optical radiation are laid down in the Finnish Government Decree on the protection of workers from risks arising from exposure to optical radiation (146/2010).
Manufacturers’ responsibilities
Manufacturers have a duty to supply their machinery with built-in lighting if there are any parts in the equipment that pose a hazard without such additional lighting. Built-in lighting in machinery must be designed specifically for the operation in question. Proper lighting must be provided especially in any internal areas of machinery that need to be accessed for inspection, adjustment and maintenance purposes.
Machinery must be designed and constructed so as to prevent any risks resulting from shadows or reflections. Moreover, any dangerous moving parts of machinery must not be susceptible to what is known as the “stroboscopic effect”, an illusion caused by lighting that makes components rotating at a certain speed appear to be stationary.
Instructions for employee
Instructions for employer
It is the employer’s duty to fit the workplace with lighting that
- suits the nature of the work
- provides enough light to allow workers to see what they are working on without difficulty
- takes into account employees’ personal characteristics (age, eyesight, any spectacles they wear and their energy levels), and
- does not pose a risk of injury due to
- glare or
- workers’ not being able to perceive that a dangerous component is moving (“stroboscopic effect”).
Enough daylight must be allowed into the workspace wherever possible.
As there are no official guidelines or limit values for lighting, the potential hazards and risks associated with lighting must be evaluated on a case-by-case basis. A specialist can be called in to assess the adequacy and appropriateness of lighting, or industry standards can be consulted to determine how workers perceive the lighting in their workplace.
Legislation
Occupational Safety and Health Act (738/2002)
- 34 §
Government Decree on Safety and Health Requirements in Workplaces (577/2003, in Finnish)
- Section 10 – Lighting of workplaces
Government Decree on the Safety of Machinery (400/2008, in Finnish)
- Section 5 – Obligations of the manufacturer or their authorised representative
- Annex I, section 1.1.4. Lighting