
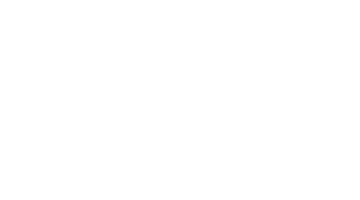
Services and contact information
Maintenance enclosure requirements
Equipment used in asbestos removal works must be cleaned and serviced in a designated space to control dust emissions.
The maintenance enclosure must be a separate room that can be ventilated so as to prevent dust from spreading to surrounding areas. Asbestos removal licence applicants are therefore required to have a negative pressure unit and suitable cleaning equipment. Alternatively, cleaning and maintenance can be
outsourced to another asbestos removal licensee.
Structure of the maintenance enclosure
The maintenance enclosure must be warm and have solid walls (made of panels, not plastic). The floor and wall finishes must be washable. At least the bottom 1.5 metres of the walls must have a waterproof finish.
There must be a water supply and a drain in the room. The drain must be equipped with a coarse filter to catch asbestos debris. The filter must be changed after every time the room is used. Filtered wastewater can also be collected in a container. The room must be signposted with asbestos warnings.
Three-stage airlock
The room must be accessed through a three-stage airlock.
Ventilation must be primarily provided through the airlock. The airlock must have solid walls. Plastic sheets can be used to separate the chambers inside the airlock. Air must be allowed to entrain through the airlock even if there is a separate vent in the enclosure.
The outer doors of the airlock must form an airtight seal in the event of the negative pressure unit malfunctioning in order to prevent asbestos dust from escaping the enclosure through the airlock.
The innermost airlock chamber must be equipped with a vacuum cleaner for clothing and a bin. It must be possible to switch the vacuum cleaner on and off inside the chamber, and there must be enough space for using it there.
The middle chamber must have at least a wash basin with running water to allow workers to wash themselves.
The outermost chamber must have a coat rack for hanging workers’ regular clothing.
Contaminated equipment can be taken into the enclosure through the airlock if there is no other entry point for this purpose. Each airlock chamber must measure at least one square metre in order to allow enough space for performing the required tasks.
Air pressure inside the enclosure must be at least five Pascals below atmospheric pressure. There must be a dust extraction arm inside the enclosure for cleaning contaminated equipment. The dust extraction arm can share a duct system with the vacuum cleaner inside the airlock.
Other entry points into the enclosure must be airtight, and it must be possible to lock them from inside the enclosure. All other entrances to the enclosure must be locked while the space is contaminated.
There must be a secondary negative pressure unit available to use in the enclosure while the main unit is being cleaned and serviced.
All air inlets in the ventilation equipment must be sealed once works are completed. The performance of the ventilation equipment must be monitored and measurements taken at least once a year.
The maintenance enclosure, the airlock and air inside the enclosure must be decontaminated after every operation involving asbestos. Decontamination must be verified by visual inspections and documented in, for example, a maintenance log.