
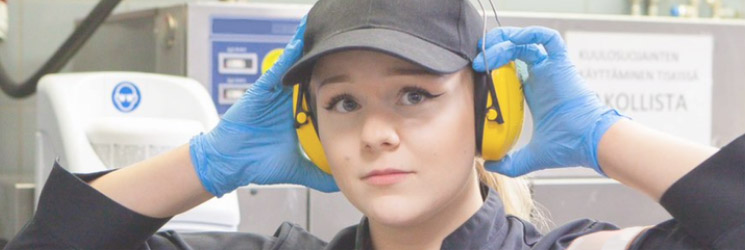
Working conditions
Reduction of risks posed by noise
As noise is known to be dangerous to workers’ health, employers are obligated by law to either eliminate the associated hazards and risks or reduce them by whatever means are typically available. The surest ways to do this are lowering noise levels immediately next to a worker’s ear and reducing the duration of the exposure.
Employers must choose the means to eliminate or reduce the risks posed by noise on the basis of the latest technology and the circumstances in the workplace. Employers have a duty to take whatever steps are necessary to reduce the amount of noise generated by their employees’ work and to prevent the noise from reaching workers’ ears. The circumstances of the workplace are usually best known to the employer and the employees themselves, while measures to reduce noise levels and protect workers generally require assistance from noise protection professionals.
Minimisation of risks posed by noise
Any identified risks and hazards must be eliminated or reduced by as much as possible. The first priority should be to lower individual workers’ noise exposure levels or to reduce the duration of their exposure to noise. The choice of measures should be based, above all, on the means listed in the Finnish Government Decree on the protection of workers from risks arising from noise, which are designed to prevent noise and reduce noise exposure. A secondary option is to provide employees with hearing protectors.
Ways to reduce exposure to noise
In order to reduce noise levels, the first step is to identify the most notable sources of potentially harmful or dangerous noise in the workplace. The employer must then look into each source of noise separately and determine whether
- the work can be performed in a less noisy way
- the work can be performed using less noisy equipment
- noise levels can be lowered by upgrading or servicing the equipment or by drawing up a maintenance programme for the equipment
- noisy operations and workstations can be positioned so as to reduce the amount of noise that reaches workers’ ears
- noise levels can be lowered by teaching workers how to use work equipment correctly and safely
- the amount of noise that reaches workers’ ears can be reduced by
- applying damping materials (such as rubber) to vibrating surfaces or reducing the area of vibrating surfaces
- preventing vibrations from travelling through the infrastructure to large surfaces
- encasing the sources of noise or noisy components
- erecting walls between sources of noise and the nearest workstations
- building a soundproof control room for the operators of noisy machinery
- adding acoustic insulation to the surfaces nearest to sources of noise or to the walls and the ceiling, or
- noise cancellation
- the work can be planned so that workers need to spend less time in noisy conditions or so that they can perform their work further away from sources of noise, or
- the work can be planned so that workers are able to step away from the noisy area at times.
The employer must implement any of the aforementioned measures that are feasible in practice and can be implemented without unreasonable costs considering the harmful effects of the exposure.
Special action required from employers
The law lays down noise exposure action values and limit values to protect workers against hearing loss, and employers have a legal obligation to take action if these values are exceeded. It is the employer’s duty to find out which of the obligations apply to them by evaluating and, if necessary, measuring the noise exposure of each of their employees.
Manufacturers’ responsibilities
Manufacturers have a duty to include information about the noise emissions of their machinery in the operating instructions. If a machine’s noise emissions exceed 80 decibels, the manufacturer must explain in the instructions how much noise is emitted by the machine to the workspace. The primary purpose of this requirement is to enable employers to choose the least noisy machinery for their employees to use. The information must therefore also be provided in technical brochures.