
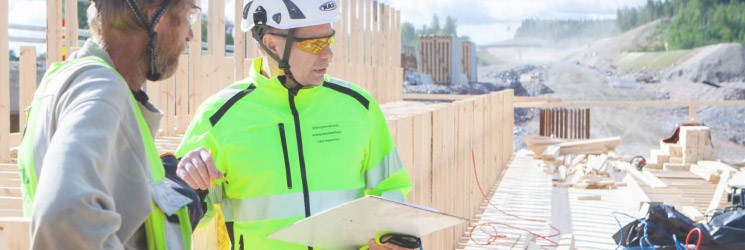
Safety and health in the workplace
Typical hazards
This page presents typical occupational risks. Risks can be detrimental to the health and safety of employees if the risks are not taken into account in workplace operations. Therefore, the employer must identify and assess the risks and reduce their potential to at least the level required by law.
There may be other hazards at the workplace than those listed here. On the other hand, there are hazards listed here that are not met at all workplaces.
Hazards of harmful strain
Harmful strain is divided into physical and psychosocial strain. Harmful physical strain can lead to the emergence of musculoskeletal symptoms and diseases.
They can be caused by, for example:
- manual lifting
- repeated movements while working
- working on the computer
- strain related to the workstation, working position and tools.
Harmful psychosocial strain, on the other hand, causes stress, which can over time result in, for example, fatigue, difficulty concentrating and eventually in difficulties sleeping and exhaustion.
Harmful psychosocial strain can be caused by factors such as:
- content of the work (e.g. threat of violence)
- work arrangements (e.g. strain caused by working hours)
- social aspects of the working community (e.g. harassment and inappropriate treatment).
Working conditions: Physical workload
Working conditions: Psychosocial workload
Hazards caused by machinery and tools
The use of machinery and tools can cause accidents. When assessing hazards, each machine shall be considered individually, taking into account at least the following aspects:
- The following should be prevented:
- access to danger zones caused by moving parts of the machinery
- contact of the limbs with moving blades of the machinery
- accidental use of machine controls
- access to the danger zone caused by automatically operated machinery when the machine is operating.
- There should be no unprotected cutting or pressing points or other dangerous factors, such as unprotected hot surfaces.
- Machines should be equipped with a device that prevents the machine from starting accidentally after a standstill resulting from a power failure or a grid undervoltage.
- Maintenance can be carried out safely.
- Machinery and equipment requiring inspection have been inspected in accordance with rules and regulations.
Working conditions: Machinery and tools
Hazards in the working environment
Fall risks always require immediate action
Falls cause a number of serious accidents and deaths at work every year. When assessing risks, particular attention should be paid to the identification of places that cause a risk of falling. Scaffolding shall be equipped with fall-preventing structures, and care shall be taken to prevent slippery conditions on walkways. Safe access must also be provided to places that must be regularly accessed for production, adjustment or maintenance.
Get clutter under control by assessing risks
Poor order and uncleanliness increase the risk of accidents and psychosocial stress due to searching for tools and unnecessary interruptions.
Internal traffic hazards are managed preemptively
A significant proportion of accidents at work occur when moving around the workplace and shifting goods. The more there are vehicles, machinery and equipment, as well as goods to be transported, the more essential it is to carefully assess the dangers and design the transport arrangements from this point of view.
With indoor climate problems, monitoring is an important part of risk assessment
Poor indoor air quality can result in, for example, symptoms of the respiratory tract and eyes, as well as fatigue and headaches. If the workplace has problems with the indoor climate, the health of employees must be monitored in cooperation with occupational healthcare, while indoor air quality must simultaneously be investigated, for example, through engineering tests, including an examination of ventilation.
Occupational health and accidents: Accident prevention
Working conditions: Work environment
Chemical, biological and physical hazards
Chemical hazards
Chemicals include detergents, solvents, oils and other liquids, as well as pharmaceuticals. Their effects can range from mild eye or skin irritation to allergies, asthma, reproductive disorders, congenital defects and cancer. The chemical risk assessment shall always be carried out in writing, and the assessment should also take into account the risk of fire and explosion posed by substances and combinations of substances. Exposure to asbestos and tobacco smoke must also be taken into consideration.
Dusts and fibres irritate the skin, eyes and the respiratory system, they can cause allergies and asthma, and at worst, they cause cancer. Dusts include wood dust and flour dust. Fibres include textile dust and glass or rock wool.
Gases, vapours, fumes and smoke must be taken into account during risk assessment. Vapour is generated when liquid material evaporates into the air, and fumes are generated when solids are treated in hot processes.
Working conditions: Chemical agents
ATEX - Finnish Safety and Chemicals Agency (Tukes)
Working conditions: Construction industry - Asbestos
Biological hazards
Biological agents include bacteria, viruses, yeast fungi, mould and parasites. Exposure may result in infection, allergy and poisoning, as well as cancer or foetal damage in case of some dangerous agents. The employer must be in possession of a risk assessment report.
Working conditions: Biological agents
Physical hazards
Noise is an unwanted sound that is unpleasant, disturbing, unexpected or harmful to hearing. In addition to hearing damage, noise can interfere with concentration and cause a stress reaction in the body, causing blood pressure, heart rate and stress hormone levels to rise. Noise can also increase the number of accidents at work.
Vibration refers to the vibration of a surface that is usually transferred from the tool to the hands or from the vehicle seat to the entire body. The results of hand vibration can include white fingertips or polyneuropathy of the hands, and as a result of vibrations in the body, lower back pain and spinal injuries can occur.
Heat work refers to working at temperatures above 28 degrees. As a result, there may be fatigue and reduced concentration, as well as heat-related illnesses such as a sunstroke, sudden dizziness, fainting, muscle cramps and, at worst, a life-threatening heatstroke. The heat also increases the strain on the heart. Certain chronic diseases and individual factors increase the risk of a heatstroke. The handling of hot objects must also be considered.
Cold work refers to working at temperatures below 10 degrees above zero. The most common phenomenon is the cooling of the hands and feet. Moderate cooling results in the declining of hand function, peripheral muscle strength and intellectual function. The consequences of strong cooling include reduced blood circulation, increased blood pressure, heart strain and frostbite. In an extreme situation, hypothermia can occur, and it is a life-threatening condition. Drafts and the handling of cold objects must also be considered.
Inadequate lighting is uncomfortable, reduces work efficiency, increases the number of errors and can also lead to accidents at work. In addition, it can lead to poor working positions as the employee must reach out towards objects to see better. Reflections must also be taken into account, as well as the fact that with age, more light is needed, especially in work requiring preciseness. Outdoor lighting and the lighting at access routes must also be assessed. The guideline values found in the SFS-EN 12464-1 standard, “Light and lighting. Lighting of work locations. Part 1: Interior lighting” can be used.
Ionizing radiation can damage cells and increase the risk of cancer. Ionizing radiation includes, for example, X-ray radiation and soil-derived radon radiation.
Optical radiation can damage the health of the skin and eyes or lead to an accident due to momentary blindness. Optical radiation includes UV radiation, visible radiation (light), infrared radiation and laser radiation.
Electromagnetic fields can cause direct effects such as dizziness, nausea and warming of parts of the body. In addition, they can interfere with medical devices such as pacemakers or insulin pumps and be harmful to pregnant employees. Electromagnetic fields are utilized, for example, in melting metals and jointing plastics, and they are also found near high-powered antennae.
Electrical work always carries a high risk of accidents. An electrical current heats the body tissues and affects the electrical functions of the body, especially in the heart and brain. In addition to electrical occupational safety, risk assessment applies to electrical equipment, hardware and installations used at work.
This website is part of the European Commission's Your Europe portal. Did you find what you were looking for?