
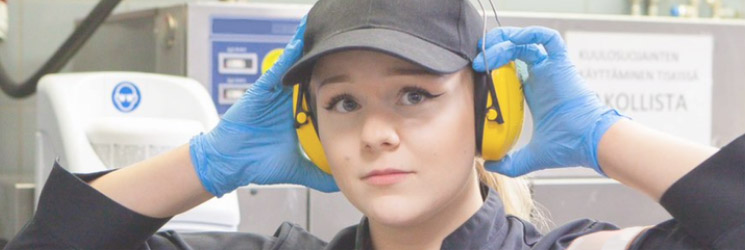
Working conditions
Internal traffic
Internal traffic and transfer of goods in workplaces
A considerable percentage of occupational accidents are related to traffic and goods handling. The employer must review and assess the risk factors relating to internal traffic and transferring of equipment at the workplace and plan and implement measures to eliminate or mitigate the hazards observed.
Well-planned internal traffic systems and goods handling procedures are vital for preventing occupational accidents.
Any vehicular and pedestrian access routes in a workplace must be clearly marked. Also other safety signs must be clearly visible. Loading docks and ramps, for example, must be clearly marked, and exit routes must be marked with visible exit signs.
Vehicular and pedestrian traffic must be kept separate
To make it safe for employees to move around, the first rule is to ensure the safety of all access routes, passageways, floors, staircases and work surfaces and to maintain good order and cleanliness in the workplace.
It is the employer’s responsibility to reserve enough space for traffic and to provide clearly signposted, separate, safe and practical routes for vehicles and pedestrians.
Special attention must be given to the safety of employees who work in the immediate vicinity of streets, roads and other vehicular routes. Vehicular routes must have sufficient visibility. In addition, sufficient space must be provided for all access routes, staircases, doors and gates, and safe routes for pedestrians.
Traffic rules help to increase safety
It is the employer’s duty to draw up internal traffic rules for the workplace if necessary. The need for internal traffic rules can be determined in the course of the risk assessment process. The assessment must take into consideration the nature of the work performed in the workplace and the volume and nature of traffic and the goods transported there.
The more internal traffic, different kinds of vehicles, machinery and equipment as well as goods in need of transport there are in a workplace, the more important it is to have an efficient traffic system in place. It is the employer’s responsibility to familiarise both their employees and any persons visiting the facilities with the traffic rules and to ensure that the rules are observed in practice.
Forklift operators need to have written authorisation from their employer in order to operate forklifts and man lifts. In addition to providing written authorisation, the employer must ensure that the employees have sufficient capabilities and skills to safely operate the equipment.
Goods must be handled using safe equipment
Employers are responsible for planning and providing their employees with safe ways to lift, transport, store, handle and load goods in the workplace. This includes, among other things, ensuring that any lifting equipment and assistive devices provided for employees are in good working order and suitable for the work in question in terms of, for example, lifting capacity.
The employer must ensure that statutory hoisting devices used at the workplace are checked by an approved specialist or an expert community.
Loads must always be properly secured, and there must be enough space to lift and move loads around. Other employees or non-authorised persons must not enter the hazard zone.