
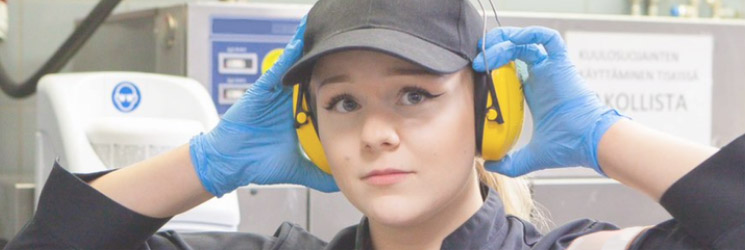
Working conditions
Quartz dust
Alveolar quartz dust (crystalline silica) is a very fine dust that enters deep into the lungs when inhaled. People get exposed to quartz in mining, the concrete industry, the glass and porcelain industry and various industrial construction tasks, among others. Quartz dust occurs in all work that involves the machining of stone-based materials.
General information on topic
Supervision of construction sites
Construction site supervision aims to ensure that no one is exposed to carcinogenic substances and that work is carried out safely. Supervision is targeted at developers, the general contractors of construction sites, employers and independent contractors.
Focus of supervision
- Dust suppression plans and their content
- Employee orientation
- Use of dust suppression methods
- Machinery and tools
- Working methods
- Compartmentation/protective walls
- Personal protective equipment
- Instructions for managing quartz dust (Finnish Institute of Occupational Health). In support of supervision.
- Use of working methods that produce less dust
- Requiring dust measurements if necessary
- Staff facilities
Order of protective measures
1. Removal
Planning and using work processes so that there is no need for work leading to exposure
2. Replacement
Replacing material containing quartz with material containing less quartz
3. Technical protective measures
Target extraction, negative pressure, dust suppression, etc. (including respiratory protection)
4. Management measures
Restricting access to the work area and providing employees training, instructions and information
5. Personal protective equipment
Last option, e.g. respirators and other protective equipment
Obligations of the developer
The developer has to prepare written procedures for the worksite, laying down the timetable for the work, requirements concerning special working methods, procedures concerning the organisation of subcontracting and the procedures concerning industrial hygiene measurements that are relevant to employers. For industrial hygiene measurements, the developer has to determine which substances are measured, by whose employers and at which work stages.
Harmful quartz-containing dust has to be taken into account in industrial hygiene measurements. The developer has to indicate whether there is a need to perform industrial hygiene measurements. If measurements are not necessary, the developer has to justify why.
In the safety document, safety rules or procedure guidelines, the developer can comment on requirements for working methods involving particular hazards, such as measures to eliminate or reduce employees’ exposure to quartz-rich dust, taking into account the work carried out at the site and other aspects of operations at the site.
In the safety document, safety rules or procedure guidelines, the developer can comment on requirements for working methods involving particular hazards, such as measures to eliminate or reduce employees’ exposure to quartz-rich dust, taking into account the work carried out at the site and other aspects of operations at the site.
Obligations of the general contractor
The general contractor is responsible for drawing up a dust suppression plan for the construction site.
For dust containing quartz, the dust suppression plan has to mention:
- the work stages with a potential of forming quartz-containing dust
- the measures to prevent the spread of quartz-containing dust.
- the need for and implementation of compartmentation.
- the dust removal methods that are used for machinery and tools.
- how accumulated dust is removed from surfaces and what equipment is used to remove dust (cleaning methods, equipment and how often).
The dust suppression plan or some other plan must specify the necessary personal protective equipment for situations where persons can be exposed to quartz-containing dust at a construction site. The plan also has to describe how workwear and tools are cleaned when an employee leaves an area with hazardous dust.
The dust suppression plan has to include instructions for storing respirators in such a way that they are not exposed to the contaminants of the construction site.
The general contractor has to:
- Explain how employees are to eliminate or reduce exposure to quartz-containing dust (e.g. requirements for machines used and measures taken to prevent the spread of dust)
- Explain the need for using respiratory protection.
- Forbid coffee and meal breaks in workspaces with potential exposure.
- Coordinating work to limit exposure to work stages that cause dust.
- Ensure (in general) that the worksite has appropriate staff facilities
- If necessary, a space with separate lockers for dirty and clean clothes.
- Staff facilities have to be cleaned daily or more often if necessary.
- Ensure the general order and cleanliness of the worksite and keep the site as free of dust as possible.
- Monitor compliance with the instructions on dust control at the worksite and intervene if issues are observed.
Obligations of the employer (subcontractor)
- Assess the hazards (risks) caused by quartz-containing dust – the risk assessment has to be done in writing.
- Organise employee orientation on safe working practices.
- Make sure that employees’ health checks are carried out on time.
- Check with occupational health care that each employee is fit for the work.
- When using temporary agency workers, the presence of quartz-rich dust in the work must be reported to the agency supplying temporary agency work.
- Employers using temporary agency work must, for their part, ensure that each temporary agency worker is fit for the intended work.
- Occupational health care workplace surveys – also worksite-specific.
- ASA register notifications of employees to the Finnish Institute of Occupational Health.
- If an employee’s exposure is at minimum 2 hours/day over 20 days or 1 hour/day over 40 days in a year. When exceeding 0.005 mg/m3 (10% of the HTP value). The use of protective equipment does not remove the notification obligation.
Dust suppression equipment for the management of quartz-containing dust
For suppressing quartz-containing dust, construction sites are required to use local exhaust vacuum cleaners with class H extraction or other local exhaust vacuum cleaners with adequate filtration capacity.
The requirement of class H extraction for quartz-containing dust suppression applies to all vacuum cleaners manufactured in compliance with standard SFS-EN 60335-2-69.
If necessary, facilities must also have adequately efficient air purifiers / negative pressure units with an appropriate filter, such as H13. The manufacturer’s instructions on filters must also be taken into account with negative pressure units.
Employees must wear class P3 respirators when doing dusty work. If necessary, respirator masks equipped with a fan must be used in heavy work stages that produce a lot of dust.
Overall, dust suppression methods must achieve a level below HTP value, and measures must be taken even beyond. A safe level is below 0.005 mg/m3 (10% of the HTP value).