
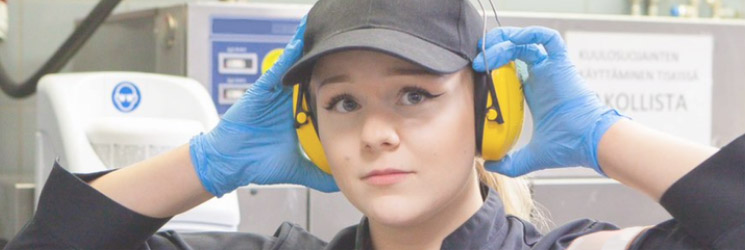
Working conditions
Manual lifting
Manual lifting and carrying are a risk to employees’ health and ability to work
As far as possible, work stages should be organised so that no manual lifting and carrying needs to be performed, being instead replaced with technical solutions. However, as some work requires employees to perform manual lifting and carrying, this is not always possible.
Strain resulting from heavy physical work increases the risk of musculoskeletal disorders and may also place strain on the respiratory and circulatory systems. Handling heavy loads also increases the risk of accidental injury. In many cases, heavy physical work contributes to early retirement.
No weight limits have been placed on manual lifting in the law. The hazards and risks caused by manual handling of heavy loads must always be considered together, as the weight of the load is only one contributing factor.
The strain caused is affected by
- the weight and shape of the load,
- the grip that can be achieved on the load,
- the positioning of the load relative to the body of the person lifting it,
- the position of the body during lifting,
- the number of lifting actions and repeated lifting actions performed,
- the distance the load is carried,
- the work environment and
- the employee’s personal physical characteristics.
Manual lifting actions should be planned carefully
The harmful strain caused by manual lifting can be reduced by careful planning of workspaces, tools and working methods. In the best case scenario, manual lifting and carrying can be avoided entirely or at least reduced.
- If manual lifting cannot be avoided, lifting and moving equipment and other assistive devices should be used. This is of particular importance when the loads are heavy, large or difficult to handle.
- Therefore, procedures should be planned in such a way that loads only need to be manually carried over distances that are as short as possible.
- Workstations must be designed and planned in such a way that the required manual lifting involves as little bending down, reaching and twisting as possible.
- Particularly, manual lifting to or from surfaces above shoulder-height and to and from floor-height should be avoided.
- Awkward lifting positions can be alleviated by means of adjustable workstations, lift tables or pallet stackers, for example.
- To ensure that loads are easy to handle, handholds must be correctly positioned and shaped and be firm and sufficiently large.
- The employer must establish whether the load’s physical attributes can be modified for purposes such as improving the grip that can be achieved on it.
Manual lifting and carrying cannot always be avoided or lightened through the use of assistive devices. In such cases, the employer must ensure that employees receive sufficient training and instruction in the safe handling of loads.
Hazards and risks of lifting
The employer must evaluate and monitor the strain caused by manual lifting. Occupational health care experts may be used to help evaluate risks and hazards and instruct employees.
The work environment also has an effect on the safety of handling loads. It may increase the risk of accidents. You should, therefore, where possible, ensure that passages are sufficiently wide and even and that the floor is not slippery. Sufficient lighting in the work environment also improves safety, and a suitable temperature reduces strain. Unfavourable temperatures increase the strain of the work. The physical strain of working in a cold environment is greater, and the risk of accidents is higher.
Similarly, the employee’s age, muscular strength and work experience affect the likelihood of risks and hazards. The strain people experience from manual handling may vary from one person to another, even when performing the same tasks. However, the strain caused by work can be reduced significantly by teaching employees correct lifting techniques.
Assistive devices must be suitable for the work in question
Hoists and assistive devices must be suitable for the job in question and the loads involved. The purposes that hoists and assistive devices are designed for can be checked in their user manuals. The best tools are those that do not slow down or complicate the work being done. Assistive devices are often left unused when employees find them to be difficult to employ. Assistive devices are being continuously developed, and it is always worthwhile to check what new devices are available.
Employees must be given instruction on the proper selection and use of assistive devices. If assistive devices cannot be used in all lifting situations, employees must be instructed on the correct and safest lifting techniques. Where necessary, work should be conducted in pairs or by several employees.